In the intricate landscape of gear manufacturing, the selection between equi-depth teeth and tapered teeth carries profound implications, with each presenting distinct advantages and characteristics. Let’s embark on a comprehensive exploration of these two tooth profiles and their applications:
Equi-depth Teeth vs. Tapered Teeth:
Equi-depth teeth maintain a consistent depth along their profile, irrespective of the gear’s diameter, while tapered teeth gradually decrease in depth from the base to the tip of the tooth.
Equi-depth gears, exemplified by the extended outer cycloid bevel gears from Oerlikon and Klingelnberg, embody equi-depth teeth. In contrast, tapered teeth are epitomized by spiral bevel gears manufactured by Gleason.
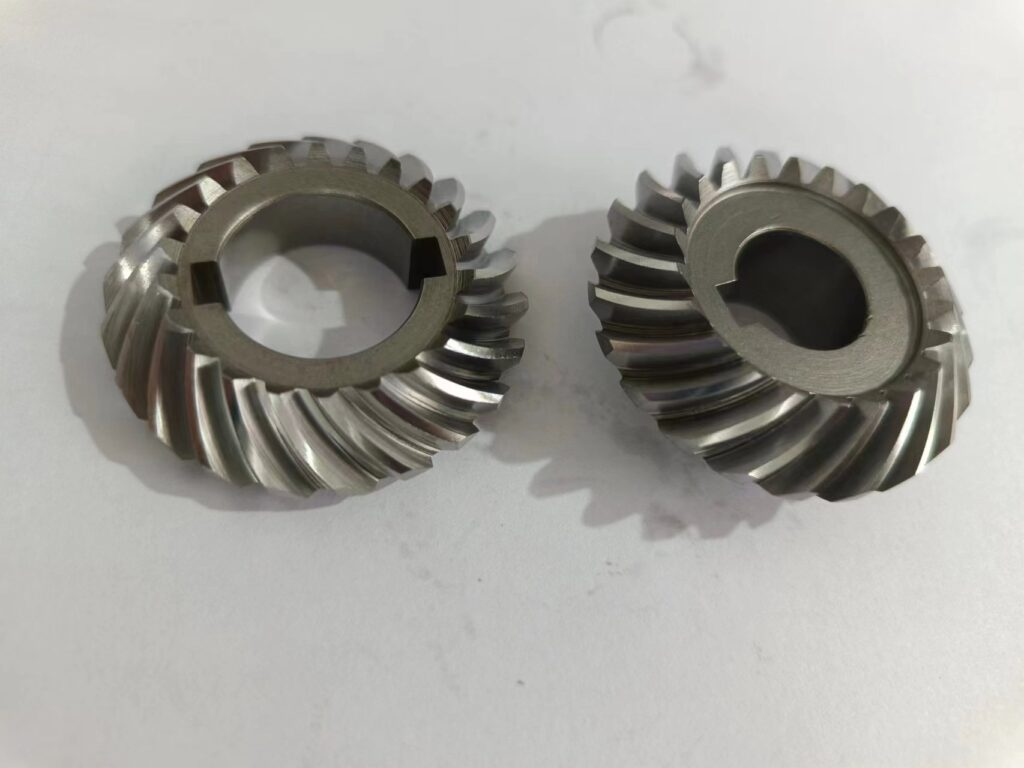
Advantages of Equi-depth Teeth:
Long Service Life: Equi-depth gears exhibit superior bending strength and contact fatigue life compared to traditional tapered tooth profiles. Gleason and Oerlikon report enhancements of over 10% in bending strength for contour tooth pinions and gears. Smooth Transmission: The pronounced curvature of the tooth line in equi-depth gears ensures stable transmission, minimizing noise and ensuring smooth operation, particularly in high-speed and heavy-load applications.
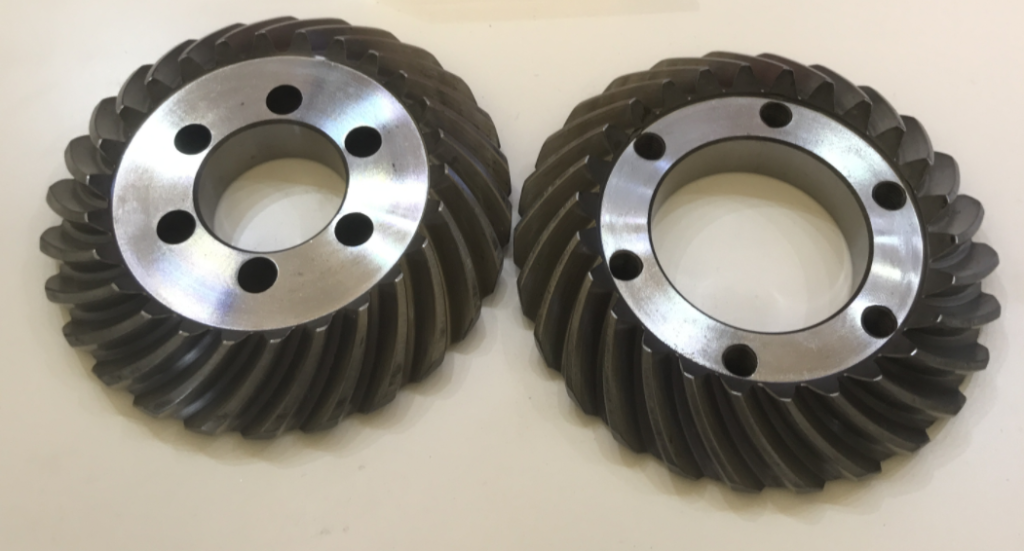
Evolution of Gear Manufacturing:
Tapered tooth profiles historically dominated the market. However, the advent of advanced six-axis CNC gear milling machine tools by Gleason and Oerlikon heralded a paradigm shift in gear manufacturing. These innovations streamlined the design and production of equi-depth gears, leading to their burgeoning adoption in industries such as automotive manufacturing.
Applications of equi-depth Gears:
Equi-depth gears find widespread utilization in leading automotive factories worldwide, including renowned brands like DaimlerChrysler, BMW, Toyota, and Honda. Their exceptional applicability and resistance to impact loads render them ideal for high-speed, low-noise automotive drive axles.
Distinguishing Features:
Machine Motion Modes: Gleason and Oerlikon systems employ distinct processing methods, with Gleason utilizing intermittent indexing and Oerlikon employing continuous indexing, necessitating an additional CNC axis for Oerlikon gears.
Tooth Surface Shapes: Gleason gears feature arc-shaped tooth lines with varying heights, while Oerlikon gears maintain a consistent tooth height along their profile.
Tool Structure and Processing Technology: Gleason and Oerlikon systems utilize unique tool structures and processing techniques, influencing efficiency and surface finish.
Tooth Surface Quality and Design Optimization: Gleason gears undergo single-sided processing, enabling individual optimization of concave and convex surfaces. Conversely, Oerlikon gears necessitate double-sided processing, presenting challenges in optimizing the contact area.
Conclusion: The selection between equi-depth (contour) teeth and tapered teeth hinges upon specific application requirements. While equi-depth(contour) gears offer heightened durability and smoother transmission, tapered teeth retain their relevance in select applications. A nuanced understanding of the disparities between these tooth profiles empowers manufacturers to make informed decisions, ensuring optimal performance and longevity in gear systems.
Thank you for reading this article, and we look forward to serving you with our exceptional gear solutions. Join our membership for more latest blogs. #BeyondGears
Read More: