With the rapid development of the wind power industry, wind turbine gearboxes have become an important research topic because they are the core components of wind turbines. The operating conditions of wind turbine gearboxes are harsh, with high power, significant speed differences, high precision requirements, long service life, and high-reliability requirements. To achieve long service life and high reliability of the transmission system, especially the gear, main shaft, bearing components, and so on, in complex working environments, strict requirements are proposed for the structural design and manufacturing processes (including material processing and surface treatment processes) of critical components.
Wind power products have high requirements for mechanical performance indicators such as surface hardness and wear resistance. In actual production, gear, shaft, and bearing components for wind power are mainly processed using carburizing and quenching. The final products can meet the specified technical requirements by employing a practical heat treatment process design. Therefore, heat treatment significantly improves the mechanical performance of wind power products.
Requirements for Heat Treatment Process Design
The performance of materials forms the basis for the load-bearing capacity of products, and the proper selection of materials and heat treatment processes can improve the load-bearing ability of wind power products. Currently, 18CrNiMo7-6 has become the mainstream standard steel for wind power products. Its characteristics are as follows:
- High core tensile strength and toughness
- High fatigue strength in the core and carburized layer
- High hardenability
- Minimal distortion after quenching
- Good high-temperature performance
The technical specifications of the product are as follows:
- Adequate carburized layer depth is 2.0-6.0mm (550HV), with deeper carburized layers being predominant.
- Surface hardness after quenching: 58~62HRC; core hardness: 30-47HRC.
- Inner oxidation depth varies according to different product carburizing layer requirements.
- Surface and core microstructure meet relevant standard requirements.
By using carburizing followed by slow cooling, reheating, and quenching processes, the performance after heat treatment meets the requirements of MQ-grade materials in ISO 6336-5. The heat treatment deformation is minimized during manufacturing to ensure consistent carbon content, metallographic structure, and hardness of the products, resulting in uniform working performance.
Carburizing and Quenching Process Curve
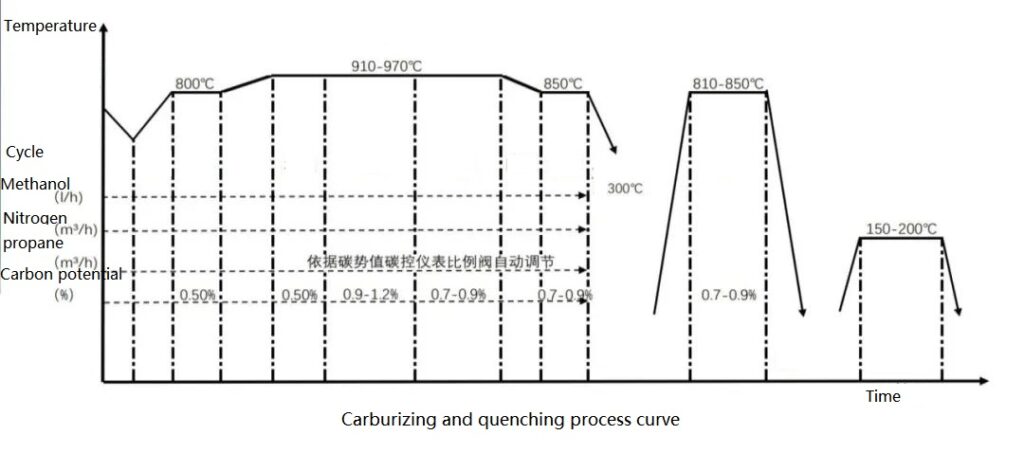
Considerations in the Production Process
Heat treatment process: Production preparation → Loading → Pre-cleaning → Gas carburizing and slow cooling + reheating and quenching → Tempering → Inspection → Packaging → Warehouse
Control of product deformation
Under the premise of ensuring the reliability, stability, and precision of the heat treatment equipment, the loading method, carburizing temperature, heating rate during quenching, quenching temperature, quenching cooling temperature, and quenching medium are critical factors affecting product deformation.
During the heating process, we adopt a preheating and stepwise heating method, and the specific preheating temperature and holding time are determined based on the product structure and loading conditions. We use suitable fixtures and proper fixture placement for carburizing and quenching products with complex systems, compensation pads, washers, and core shafts. The quenching process can utilize hot oil to achieve uniform heating and cooling of the product, allowing for a balanced temperature distribution between the core and surface and various parts of the product. The goal is to minimize temperature distribution differences.
To control the internal structure of the product during the machining process
To control the internal structure of the product during the machining process, it is essential to carefully select the heat treatment parameters such as temperature, holding time, and carbon potential. Strict control of the carbon concentration on the surface of the workpiece is also crucial.
From a heat treatment perspective, the size of the austenite grains before quenching, as well as the austenitizing temperature and time, and the surface carbon concentration, are influenced by the original structure of the workpiece before the heat treatment process. Higher austenitizing temperatures and longer times result in larger austenite grains. Moreover, when the surface carbon concentration reaches a certain level, excess carbides dissolve into the austenite, promoting the growth of austenite grains and leading to coarse martensite structure after quenching. This can also increase the amount of retained austenite.
The quenching temperature significantly affects the deformation of the product. Therefore, it is advisable to choose a relatively low quenching temperature while ensuring that the resulting structure meets the required standards.
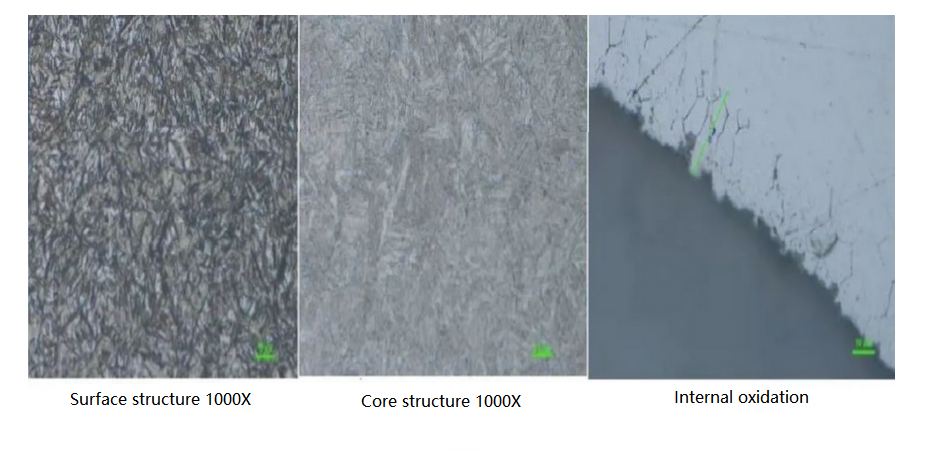
Check here to know more about material and heat treatment.
Thank you for reading. Join our membership for more latest blogs.