History of Gear Accuracy Standard
The development of gear accuracy standard began in the early 19th century, when the first precise machines for making gears were developed.
Over the next century,the standard for gear accuracy was continually refined and improved. During that time,many countries had their own gear accuracy standards and the international gear standards were not uniform.
In the early 1980s,the International Organization for Standardization (ISO) developed a set of standards for gear accuracy.These ISO standards were based on the AGMA standard and provided a more comprehensive and detailed set of requirements.
Today, the ISO and AGMA standards are widely used and accepted as the industry standard for gear accuracy.
Gear Measurement Result Analysis
Properly testing the accuracy of gears is essential to identify any potential defects or inaccuracies,so that we can ensure they meet the levels of quality and performance.
About the measurement errors,there are 3 common situations:
- Tooth error
- Tooth Profile Deviation
- Helix deviation
Tooth Errors
1. Large ƒi” and Uniform Tooth-to-Tooth Errors
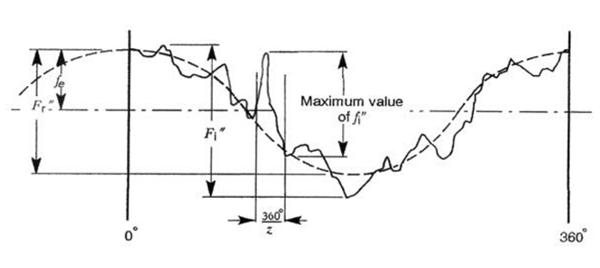
1.1 The large ƒi” is typically a dirty condition or a nick on a gear tooth. Nicks are normally caused by material handling problems. Adding a tip chamfer to the design of the gear tooth profile,and hob, will reduce this type
of damage.
1.2 a uniform but excessive tooth-to-tooth error that repeats each 360°/z (where Z is the number of teeth in the part) is typically caused by the cutting tool and involute error.
1) The hob has not been mounted correctly,or the hob arbor is damaged.
2) The hob has been sharpened in correctly.
3) poor quality hob.
4) the hob was shifted beyond its useful face width and is no longer generating the involute correctly. This may occur on one flank and will thus indicate an error in one direction of rotation.
1.3 Tooth-to-Tooth error can be caused by the hobbing machine.
a) The hob spindle has axial or radial runout.
b) End support for the hob arbor is damaged or worn.
c) Improper installation of index change gears on a mechanical hobbing machine.
2. Non Uniform Tooth-to-Tooth Errors
1) The hob is worn.
2) The hobbing machine work spindle index drive system is damaged,worn,or has excessive backlash.
3) The index change gears are damanged or installed improperly on a mechanical hobbing machine.
3. Large Fi”
1) the work piece blank has radial run-out or the blank has face wobble,resulting in excessive axial runout.
2) The work piece mounting fixture has radial or axial runout.
3) The gear teeth have excessive lead varation.
4) The hobbing machine work spindle or index drive system is worn or has runout.
4. Once per revolution non uniform error
Once per revolution non uniform error
1) The index change gears are damaged or installed improperly on a mechanical hobbing machine.
2) The hobbing machine work spindle or index drive system is worn or has runout.
Tooth Profile Deviation
1. Profile inspection with negative tip tooth.
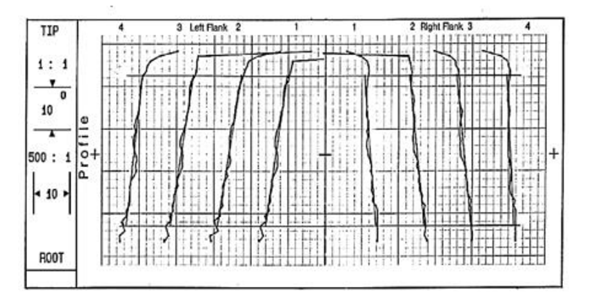
1) Incorrect hob sharpening. The hob has been sharpened with positive rake error making the hob tooth 2) larger toward the outside diameter and the gear tooth smaller.
3) Incorrect swivel angle setting on the hobbing machine.
4) Bad hob.
2. Profile inspection with positive tip tooth
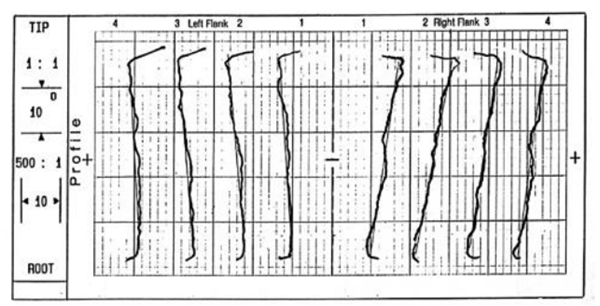
1) Incorrect hob sharpening. The hob has been sharpened with negative rake error,making the hob tooth smaller toward the outside diameter with gear tooth larger.
2) Incorrect swivel angle setting on the hobbing machine.
3) Bad hob.
3. Profile inspection with leaning tooth
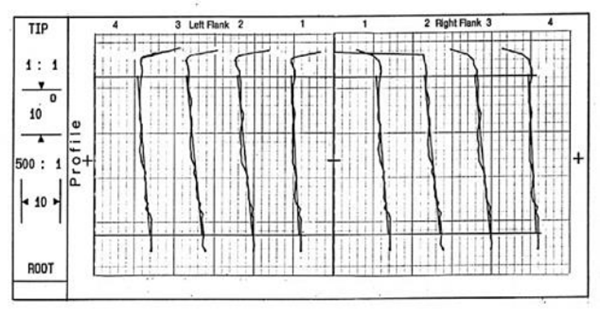
1) Incorrect hob sharpening. A hob sharpened with gash lead arror with cause both a leaning profile and size change as the hob is shifted.
2)Loose hob head swivel on the hobbing machine.
4. Profile inspection with Non-uniform wave
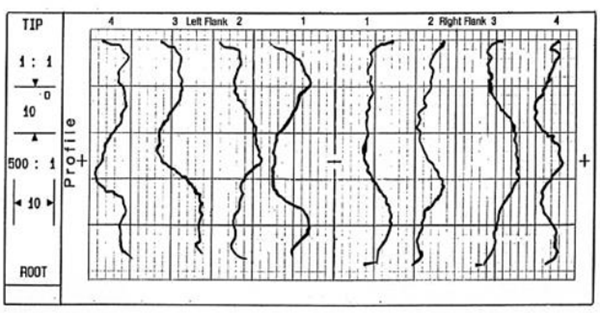
1)A loose or worn hob arbor end support on the hobbing machine.
2)Excessive backlash in the hob spindle system on the hobbing machine.
3)Excessive backlash in the work spindle system on the hobbing machine.
4)Hobbing machine system in poor overal condition.
5. Profile inspection with uniform wave
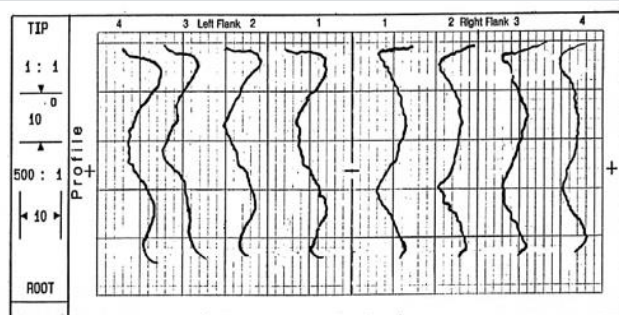
1)Hob had runout when mounted. The hob run-out can be caused by a bad cutter,damaged arvor,or dirty mounting conditions.
2)Incorrect hob sharpening. The hob was sharpened with runout during the mounting on the sharpening machine or sharpening arbor. Extreme gash to gash spacing error on the hob.
3)A loose or worn hob arbor end support on the hobbing machine.
4)Excessive backlash in the hob spindle system on the hobbing machine.
5)Excessive backlash in the work spindle system on the hobbing machine.
Helix deviation
1. Helix inspection with wobble
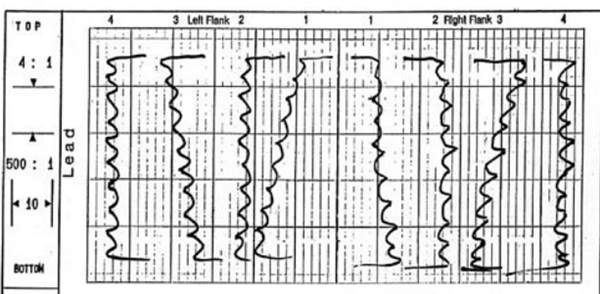
1)Part blank bore is not perpenticular to the face of the blank.
2)Part blank faces is not parrallel.
3)Fixture is not accurate or misaligned.
4)Tailstock misaligned,or center loose or damaged on the hobbing machine.
5)Inspection arbor problem.
6)Worm spindle bearing problem on the hobbing machine.
2. Helix inspection with taper
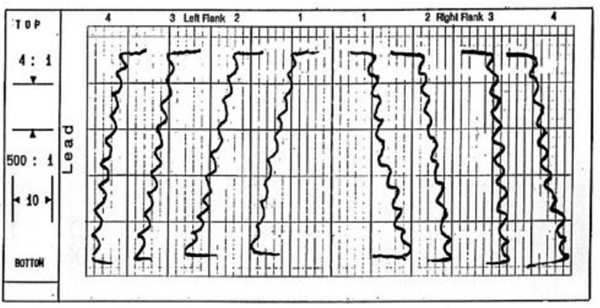
1) Tailstock misaligned on the hobbing machine.
2) Hobbing machine misaligned.
3. Helix inspection with angular error
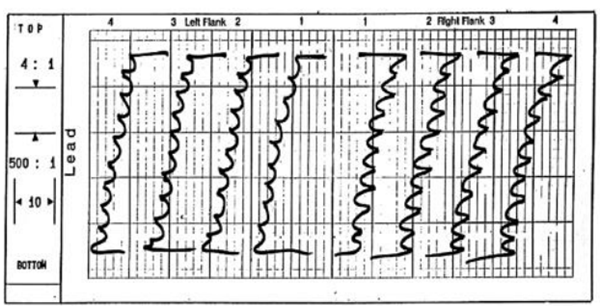
1)Tailstock misaligned on the hobbing machine.
2)Hobbing machine misaligned.
3)Incorrect differential change gears or helix value(CNC)
4)Loose or work hob arbor end support on the hobbing machine.
5)Incorrect helix checking machine seeting.
4. Helix inspection with breakout error
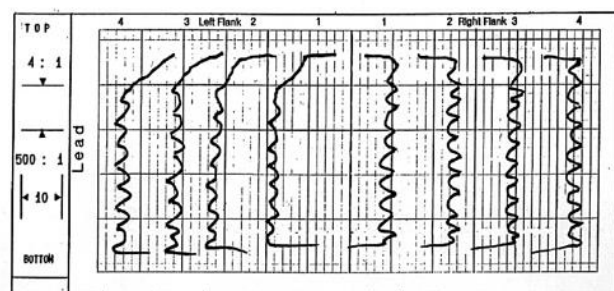
1) Tailstock loose or worn.
2) Part slipped in the fixture.
3) Fixture not clamped properly.
4) Hob arbor end support improperly installed or worn on the hobbing machine.
5) Hob saddle gibs out of adjustment.
6) Backlash in the cutter spindle drive system in the hobbing machine.
7) Backlash in the work spindle drive system on the hobbing machine.
5. Helix inspection with periodic error
1) runout of multiple thread hob.
2) thread to thread spacing error on multiple thread hob.
3) Feed screw or bearings of the feed screw on the hobbing machine.
Thank you for reading. This article was written by Doctor Shi Zhaoyao and translated by Penny Peng.